Program overview
Positioning control and collision avoidance systems for overhead cranes, travelling cranes and gantry cranes utilize wireless pulse ranging technology to achieve high-precision positioning, early warning through real-time monitoring of the distance and automatic adjustment of the state to prevent collision, and are widely used in logistics, warehousing, manufacturing, metallurgy, electric power and other industries. Especially in scenarios that require frequent movement and positioning of overhead cranes (e.g., automated warehouses, production lines, etc.), these systems can significantly improve the operational safety and stability of overhead cranes and reduce the possibility of accidents. Positioning control and collision avoidance systems for overhead cranes, traveling cranes and gantry cranes are important equipment to ensure the safety of industrial production. Through the use of advanced wireless pulse ranging technology, high-precision sensors and intelligent control algorithms, these systems can realize real-time positioning of overhead cranes and collision avoidance warning, providing reliable protection for industrial production.
Application areas: can be used for overhead crane positioning, bucket wheel machine positioning, tracked equipment positioning, gantry crane positioning and so on.
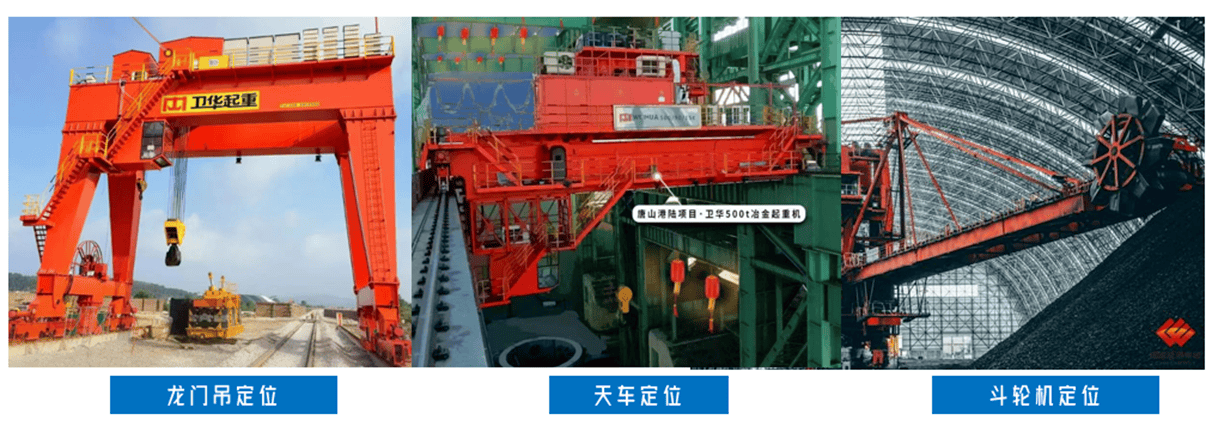
Program features
- Positioning accuracy of 10 centimeters with no cumulative error;
- 365 days * 24 hours continuous work;
- Installation is quick and easy to power up and work;
- Industrial grade design protection class IP67;
- Unaffected by dust, vapor, rain and snow.
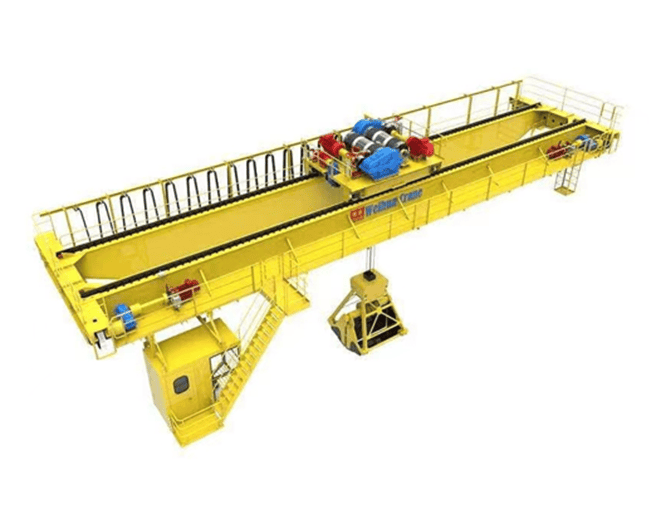
system architecture
The crane positioning system mainly consists of the origin ranging terminal and the ranging terminal installed on the crane, and the data is given to the server or PLC through 485 or RJ45.
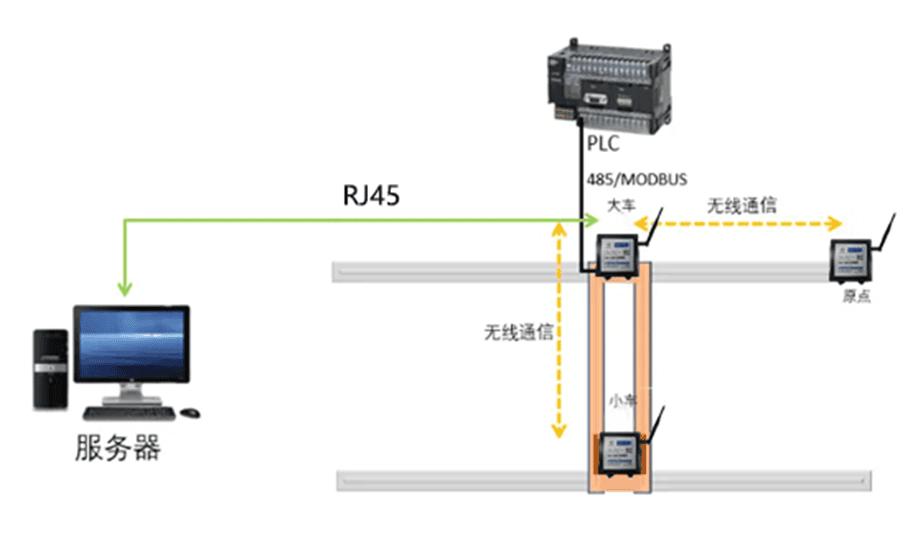
Usually, if we need to locate a small car of an overhead crane, we need to install 3 ranging base stations, if we only locate a large car as long as the installation of 2 can be, generally in the starting point of the overhead crane track to install one as the 0-point, in the large car to install one, the large car and the starting point of the ranging will be able to get the large car in the track of the distance, this distance can be marked as X, the small car and then install one, through this and the large car ranging to get the small car in the large car track distance, we mark as Y. This way we get the real-time XY coordinates of the crane. By measuring the distance between this one and the big car, we can get the distance of the small car on the track of the big car, which we can mark as Y. In this way, we can get the real-time XY coordinates of the overhead crane.
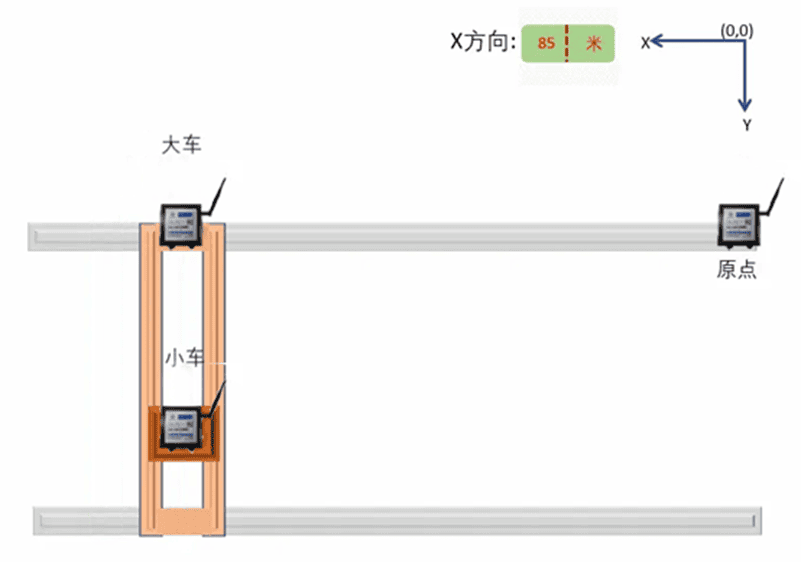
Introduction to the principle of overhead crane positioning
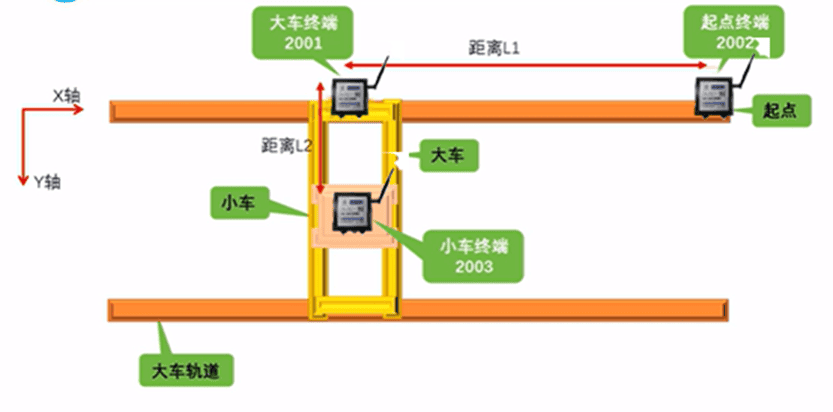
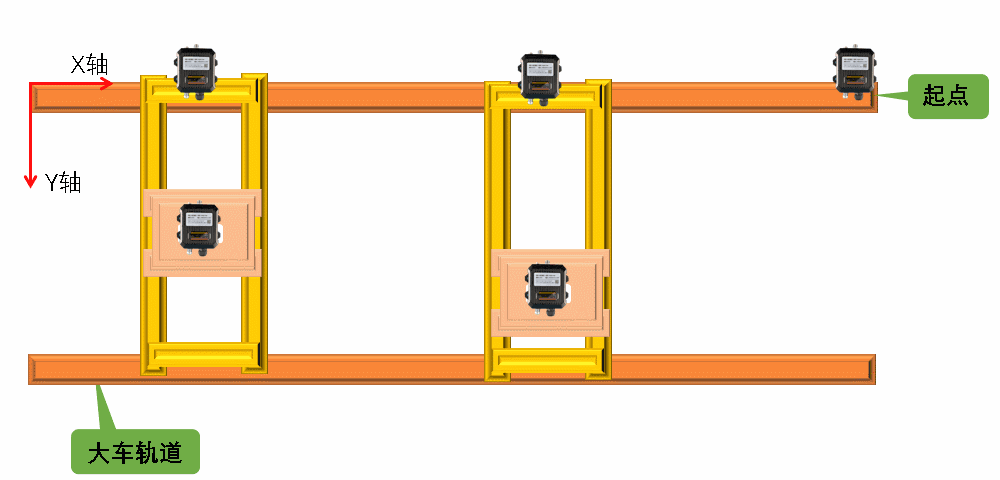
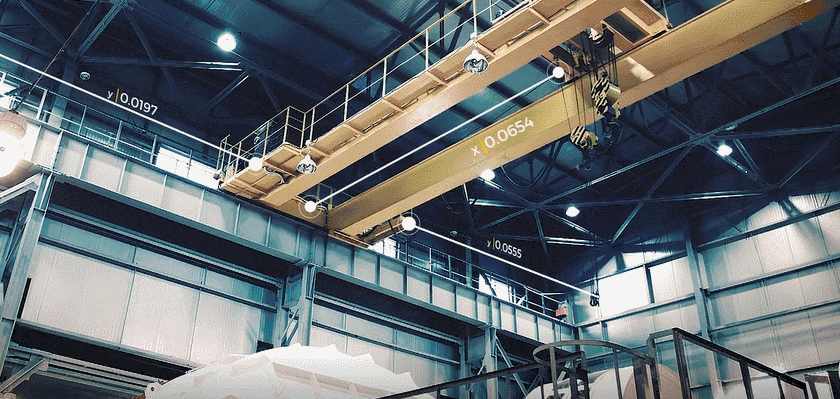
Principle of crane hook positioning
What do we do if we need to locate an overhead crane hook?
The crane hook is moving with the trolley and it is not possible to install the equipment by direct power supply. At this time, we use our battery-powered ranging tags to install the tag on the hook and obtain the real-time height of the hook by real-time ranging of the tag and the terminal on the trolley.
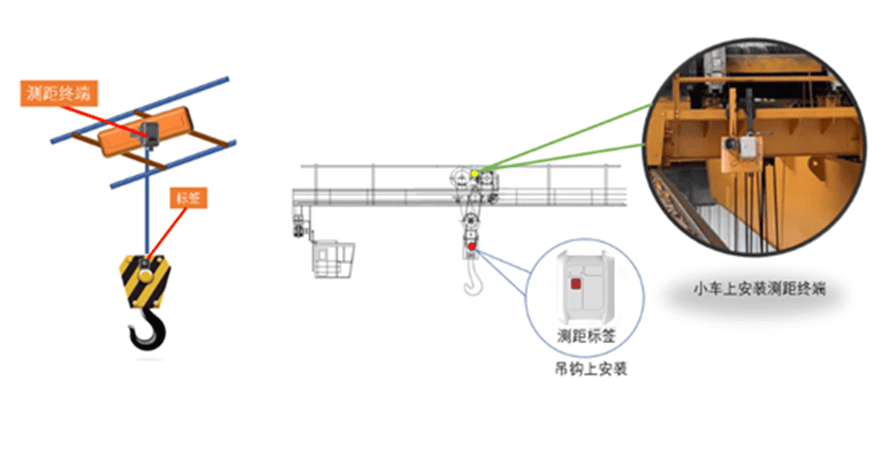
As shown in the picture, is our distance measuring tag, the tag is powered by 750 mAh rechargeable lithium battery, 1 Hz frequency can work continuously for more than 1 month, IP67 waterproof and dustproof grade design, the back of the tag can be strengthened with magnets, which can be directly adsorbed and fixed to the metal surface.
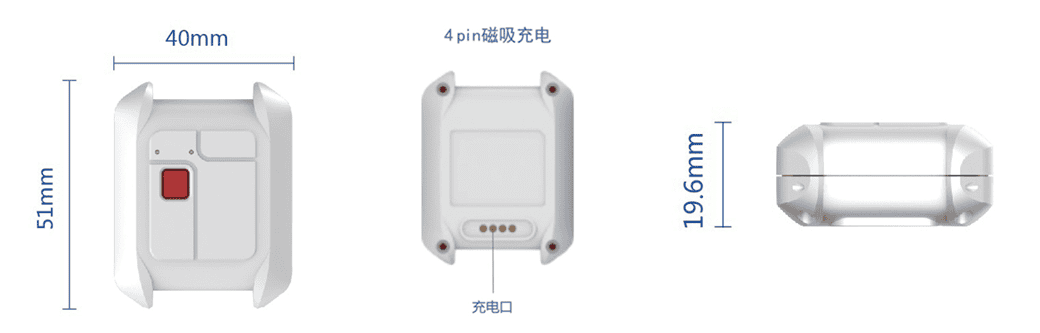
Precautions for installation of overhead crane positioning terminals
First, before going to the site to install the need to prepare in advance the installation bracket, power supply line, electrical tape, installation of screwdrivers, wrenches, vise, debugging laptop and other tools;
Second, you need to prepare the antenna mounting bracket riser in advance, the bracket riser is used to install directional antennas, the bracket height is recommended to be not less than 0.5 meters;
Third, the terminal antenna installation requirements, mutual ranging directional antenna is best at the same horizontal height, because the measured distance is the distance from the antenna to the antenna, so the requirement of ranging antenna between the center of the relative;
Fourth, the antennas ranging each other need to be visible to each other, with no occlusion in between;
Fifth, to ensure the best positioning, the antenna requires a distance of 40 cm or more between the antenna and the wall or metal surface.
Installation requirements for mutual ranging between the antennas in the same horizontal plane, large car directional antenna 2, towards the origin directional antenna one; large car directional antenna 3, towards the small car directional antenna 4, the origin directional antenna one, towards the large car directional antenna 2, the small car directional antenna 4 towards the large car directional antenna 3.
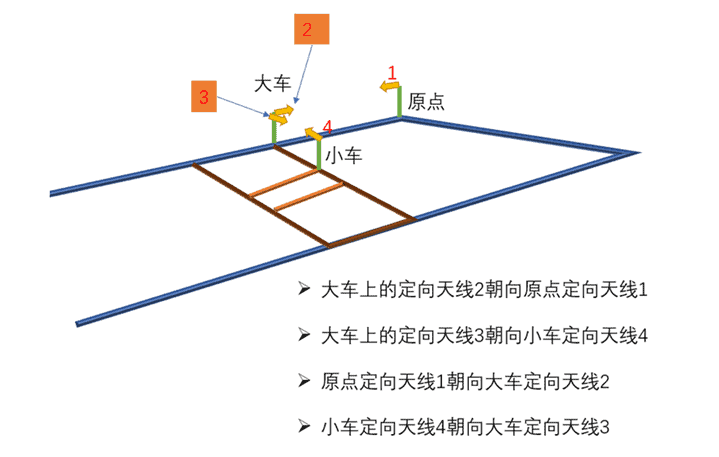
Content Reviewer:Jimme Yao