Background and needs
Manufacturing is the foundation of the real economy and the key to high-quality economic development in the future. The use of digital technology to develop a smarter, more sustainable and more resilient manufacturing industry has become a strategic consensus among countries around the world to promote economic development.
As a new management mode in the manufacturing industry, the lineside warehouse runs through the whole production process of the enterprise. In some typical discrete industries such as daily chemical production, electronics manufacturing, home appliance manufacturing and other industries, the factory daily production of a wide range of products, in order to ensure that the production line work uninterrupted, it is necessary to all the materials in the factory and to be processed and packaged semi-finished products, finished products of the type, attribute, the location of the precise control, in order to the production line to make the correct judgment of the production state, reasonable arrangements for the production task, the deployment of materials, the purchase of new In order to make a correct judgment on the production status of the production line, rationally arrange the production tasks, allocate materials, purchase new raw materials, and prevent the unused residual materials from piling up and wasting the limited space of the production line, so the digital management of the wire-side warehouse came into being.
1 ,prescription
Based on UWB IoT technology to provide accurate positioning solutions for wire-side warehouse materials, composed of ink screen positioning tags, positioning base station, computing engine and application platform. Positioning base station through the POE switch power supply plus data return, through the convergence switch will positioning system collection end of the collected data aggregated to the server, the server installed position solution engine LS1000 will be collected through the algorithm analysis of the data to get the location of the label, and forward the data to the WPAS location data application platform.
Through the data integration with the existing SAP, RTCIS and other systems in the factory, the construction of a business platform for centralized processing of big data, efficiently and accurately realize the integrated planning of materials and production sequencing, and greatly reduce the production stagnation due to the lack of materials and production scheduling conflicts, which affects the output. On-site and combined with the configuration of large-screen monitors and handheld tablets, the overall use of the system experience has been greatly optimized, no longer confined to the office and in front of the computer, to enhance the efficiency of front-line staff and effectively reduce communication costs.
2. Introduction to the program
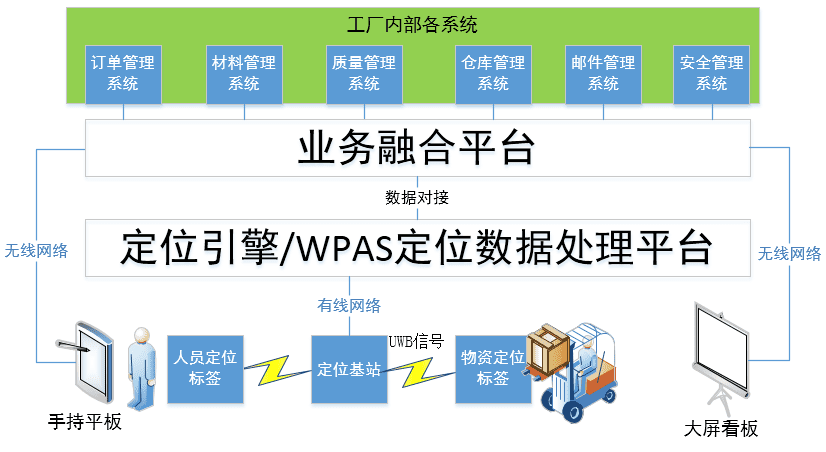
2.1 Workin-plantmaterialIntroduction of operation flow
The traditional mode of material operation in the factory is to send the order demand by hand, the warehouse receives the dosage, and flows to the production supply line through many areas, lacking the management of the intermediate flow process, and the use of paper labels to print the material information and quantities, which is a waste of consumables and manpower. In order to enable front-line staff to quickly access the latest state of the material changes, saving paper resources, etc., the use of UWB positioning labels with ink screen to fully replace the original paper labels, to obtain all the material and product information on the spatial location of the information and order information, so that the information at a glance, so that the coordination of the coordination of various departments more smoothly, so that the lack of material less material to do early warning procurement of materials, combined with the production line production, the degree of urgency of the order, material co-ordination planning reasonable arrangements for the production of line, the degree of urgency of the order Combined with the production line production, order urgency, material co-ordination and planning to rationalize the production order, enhance the efficiency of the material flow in the factory line side library. The following is an introduction to the main use of labels in the factory and the process of reuse:
(1) Binding of materials into the factory
As shown in the figure below, when the new material into the factory, first of all in the designated location of this batch of material information into the system, production work order number, and then take an unused location tag with the work order number for binding operations, the tag is placed on the material pallet board, and thereafter, in the system, the location of the tag that is the position of the material as a batch of information to use as the location of the material, at the same time the system will be the batch of material basic information down to the tag ink screen display, to facilitate employees to view. It is convenient for employees to view.
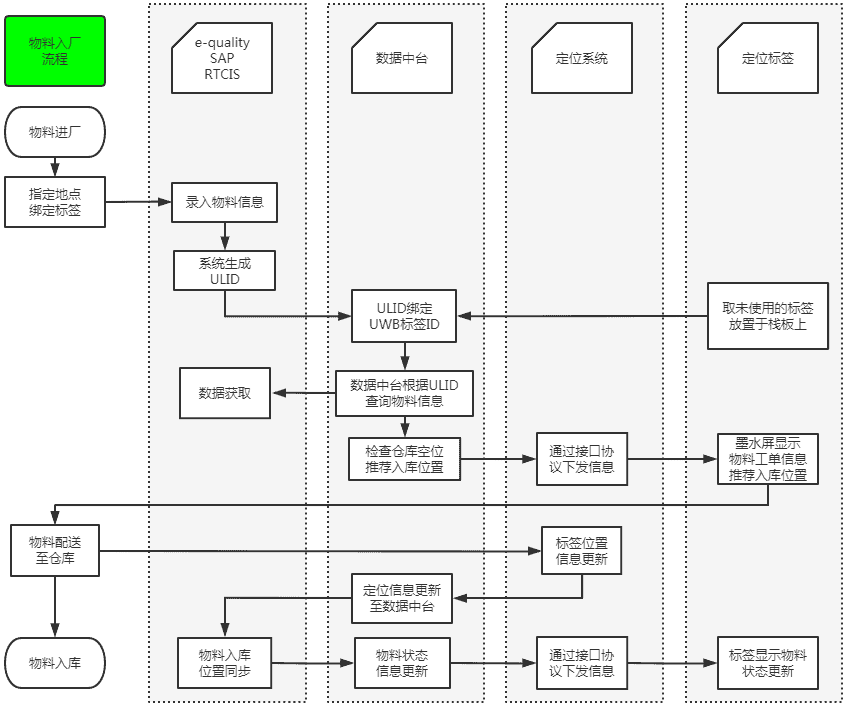
(2) Binding of semi-finished products
The production of semi-finished products also need to bind the label into the warehouse temporary storage, waiting for the processing of finished products, and materials into the factory to bind the different places mainly in the binding mode is the first-line production staff through the hand-held tablet access platform, convenient and fast, anytime and anywhere can be operated.
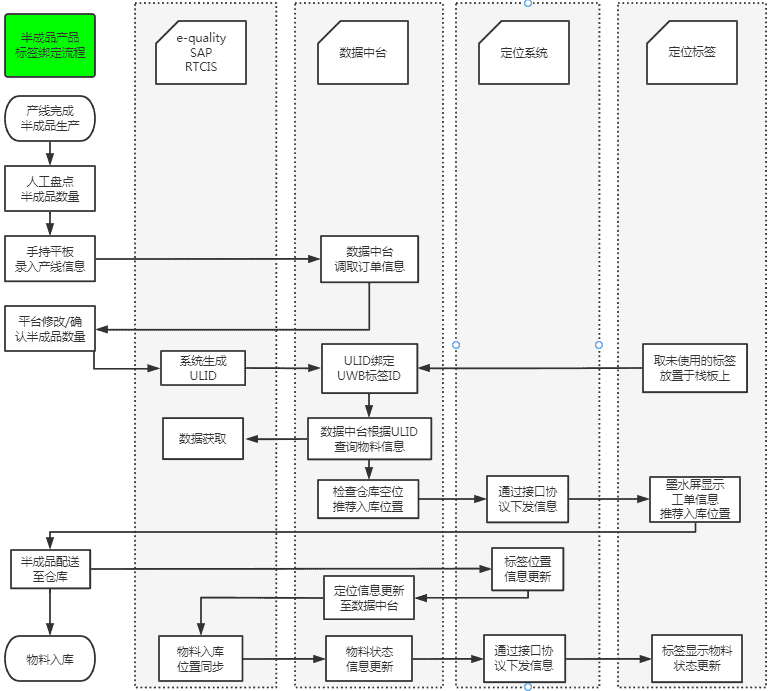
(3) Production line material requirements management
Before the production starts, the positioning system can obtain the information and quantity of the existing materials near the production line, compare the quantity in the order demand, and determine whether it meets the production requirements, and automatically notify the person in charge of the preparation of materials by e-mail when the spare quantity is insufficient to reduce the waiting time between order switching, and improve the production efficiency by reducing the downtime of the line.
Warehouse material preparation staff can also quickly lock the need to prepare the material storage location through the positioning system, reducing the time to find materials, you can improve the efficiency of the workshop and warehouse work at the same time.
It can also intelligently and flexibly adjust the number of days of material preparation according to the vacation situation of the staff in the relevant positions, so as to avoid accidental losses caused by work negligence.
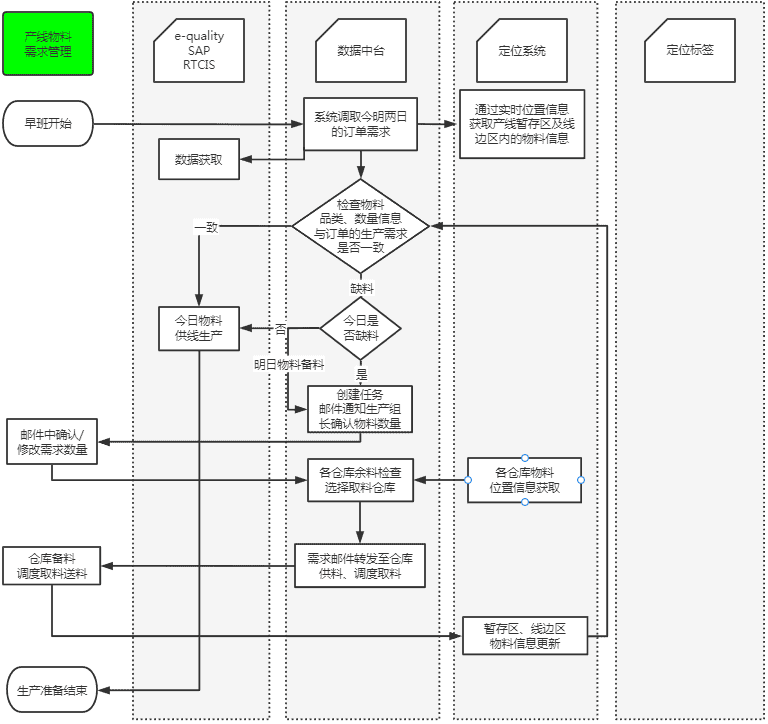
(4) Label recycling process
The electronic label replaces the paper label's advantage in addition to the information display aspect, but also can be reused benefit, when the last batch of material consumption is finished only need to put the label into the designated recycling place can be used again, at the same time the history of use record in the database can still be traced back to the query.
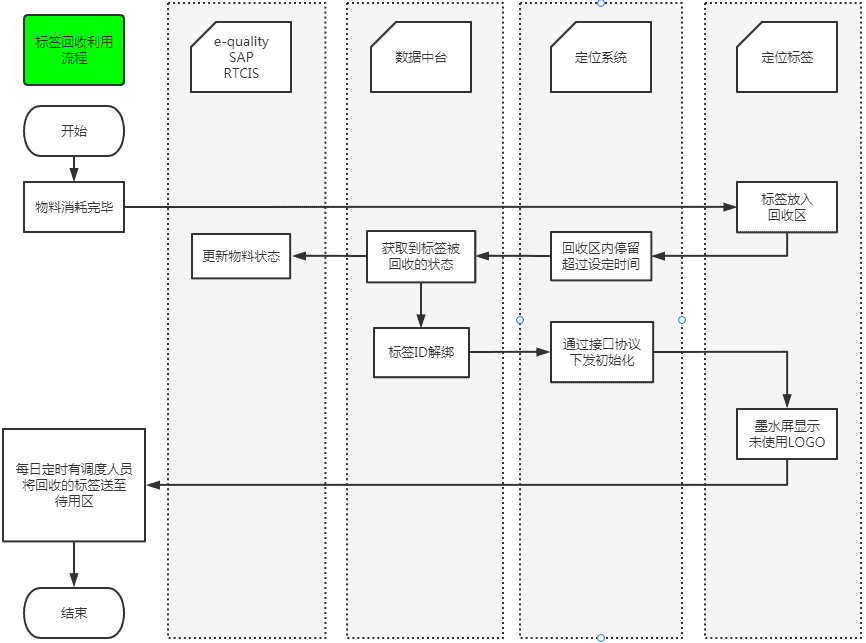
2.2business function
By binding each batch of material and product information with UWB ink screen positioning tags, it realizes the monitoring and tracking of material location and flow information in warehouses and production workshops.
Through accurate positioning, it realizes the flow tracking of materials on the shovel plate in many areas, such as in-plant warehouse, workshop pause area, workshop line-side warehouse, production supply line, and so on. At the end of the material flow, the positioning tags will be recovered and reused.
Through the big data collection of useful data from various subsystems for global integrated processing, using algorithms to calculate the rate of consumption of materials, combined with the existing inventory to determine the preparation time in advance and email notification to the relevant responsible person.
Realize the construction of factory big data platform, combine and apply the data silos of each sub-system, play the business value of 1+1>2, optimize the management and operation process, and save the company's resources.
3. Customer value
-In and out of the warehouse paperless, reducing the action of printing labels, sticking labels, modifying labels;
- Depot managers have reduced 201TP by more than 3T;
- The transparency of the warehouse has greatly improved the efficiency of the outgoing warehouse, and the time to change the line has been shortened by more than 20%;
4,Field Application Pictures
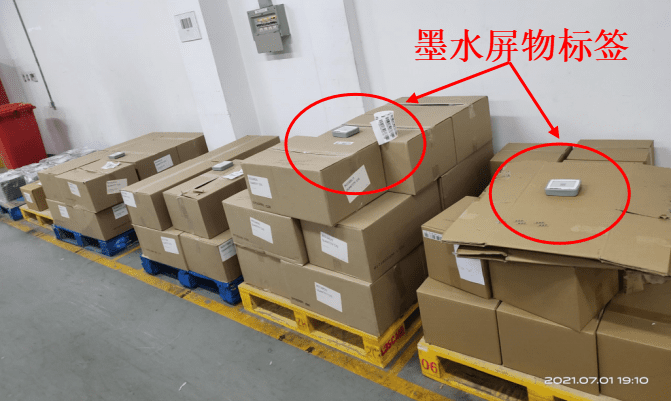
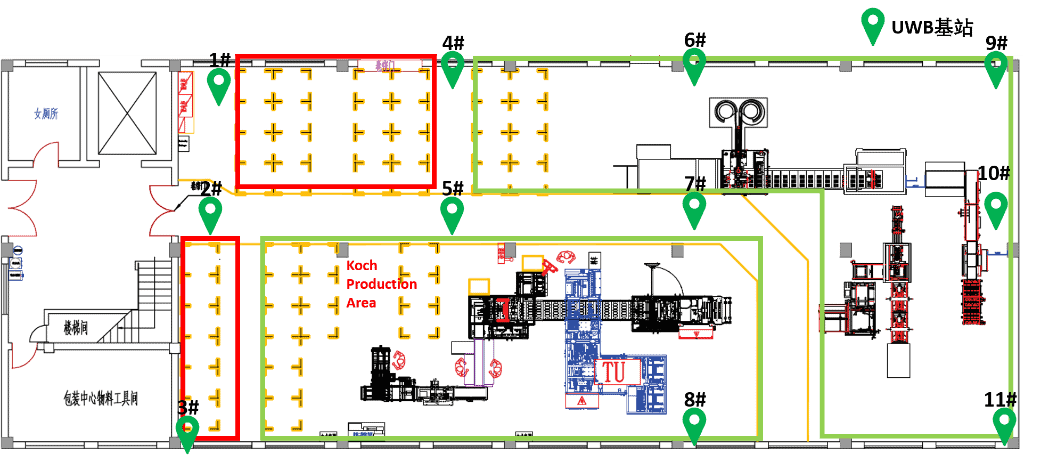
Related Products
Content review.