Pain points and needs of vehicle production plants
Pain point 1: Lack of electronic means of collecting information:
Most of the inspections, production progress surveys, and production completion surveys occur at the production site, and manually recording the data and returning to the computer to enter it creates delays and error rates in the data. Data collection, data storage, data continuity and traceability are insufficient.
Demand 1:In the face of heavy information collection work, the traditional way of relying on manual collection has been unable to meet the increasingly accurate information collection needs of enterprises, the need for electronic data collection and storage to ensure the continuity and traceability of quality data. If the UWB positioning information collection method is added, it can real-time monitor the location of production vehicles in the designated area and count the number of vehicles and record the time of entering and exiting the workstation to generate electronic reports, i.e., it ensures the real-time data and avoids the error rate of the data statistics.
Pain point 2: High error rate of vehicle information collection when production plan is temporarily adjusted:
Automotive offline vehicle inspection involves numerous workshops, including: pressure retention workshop, damping workshop, four-wheel alignment, offtake delivery inspection, offtake static/dynamic inspection and other workshops. These many workshops inspect the quality of car body manufacturing from different processes. How to satisfy the omission or error of data recording caused by the temporary production schedule adjustment within the company, and ensure the accurate recording of vehicle manufacturing information for the quality control department, which is the main problem faced by the company at present.
Demand 2:The positioning label is installed in the front file position of the vehicle and associated with the vehicle barcode, which can quickly record and find the position of the vehicle. Change the electronic fence through the platform to change the supervision area directly, realizing the intelligent recording method of immediate change and use.
Pain point 3: Lack of capacity information collection tools makes it difficult to analyze production efficiency:
For the capacity imbalance problem in the body manufacturing process, it is time-consuming to process and analyze a large amount of vehicle production information retrospectively before arriving at a preliminary result.
Demand 3:In order to monitor the production efficiency, it is necessary to count and calculate the time consuming time of each process from the source of production, which consumes huge cost of manpower, material and time. the vehicle production report function of the UWB positioning system can accurately record the length of stay at each station and the number of vehicles produced in the workshop, so as to reduce the time of the car on the production line through capacity optimization and to improve the manufacturing efficiency and delivery efficiency of the vehicle.
Pain point 4: Misuse of tools creates potentially undetectable hazards
Problems with vehicles being a safety risk due to incorrect use of tools during the manufacturing process of automobiles leading to improper installation of vehicle parts.
Demand 4:In the use of the tool binding positioning tags, each tool must be used in the designated workstation, when the tool binding tags out of the designated work area, the vehicle production management system sends a command to the tool, so that the tool function is disabled.
World PowerdevelopedUWB positioningThe product can be well used for the management needs of the automobile manufacturing industry, and has already been proven in a number of companies.
Contacts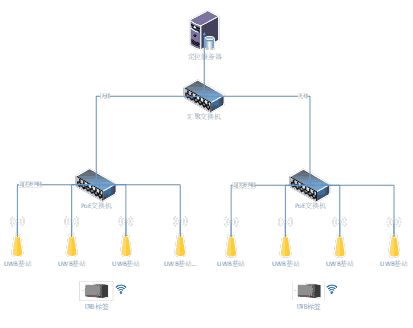
Program features
1. Higher positioning accuracy: LOS (line of sight) average accuracy is better than 30cm, NLOS (not line of sight) average accuracy is better than 50cm;
2. Longer coverage: visual coverage distance of 80-100m;
3. More flexible networking: wired & 5.8G Wi-Fi flexible collocation;
4. Stronger stability: MTBF≥10000h;
5. Larger system capacity: single-area label capacity is greater than 900, system label capacity is greater than 20,000, and can be expanded according to demand;
6. Multi-sensor fusion: Support various types of sensors such as pedometer, heart rate, barometric pressure, etc., as well as BLE and other fusion positioning, to realize multi-sensor data acquisition, processing and mining;
7. Many mature project cases: complete and mature program system, the program has been widely used in Yutong Bus, Volkswagen and other projects.
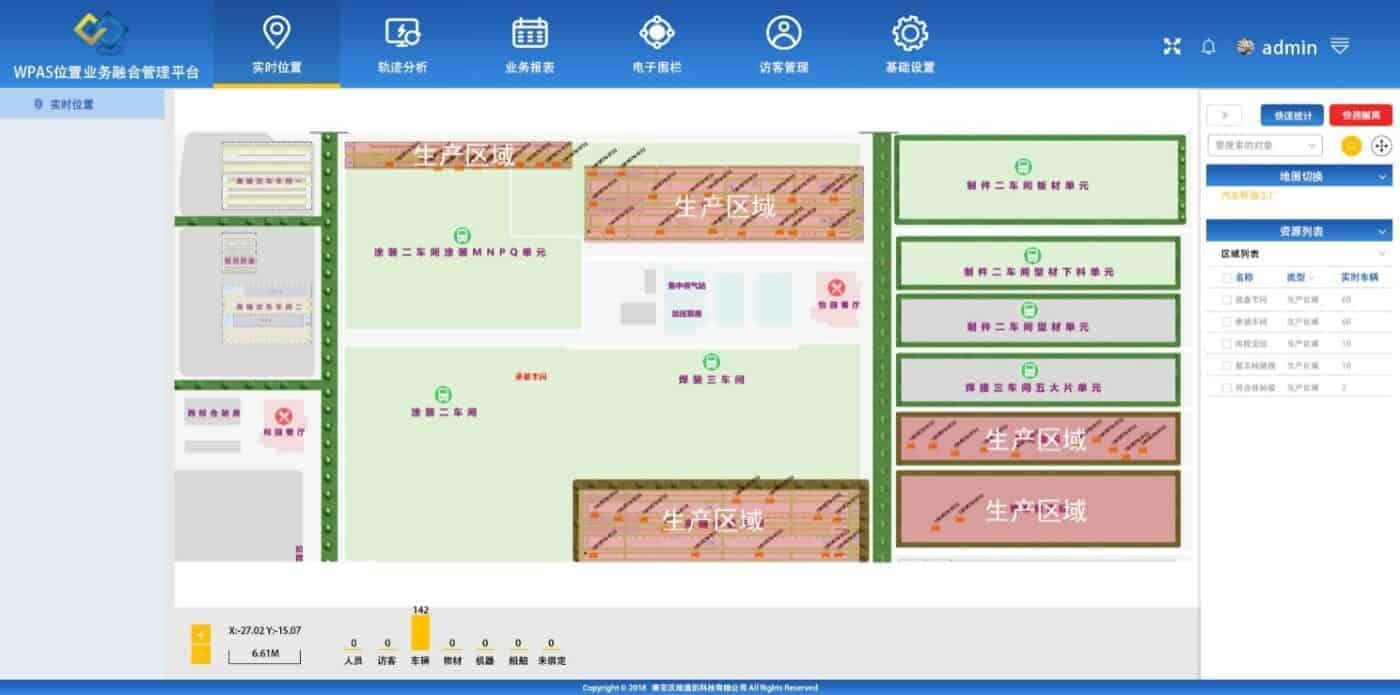
electric fence
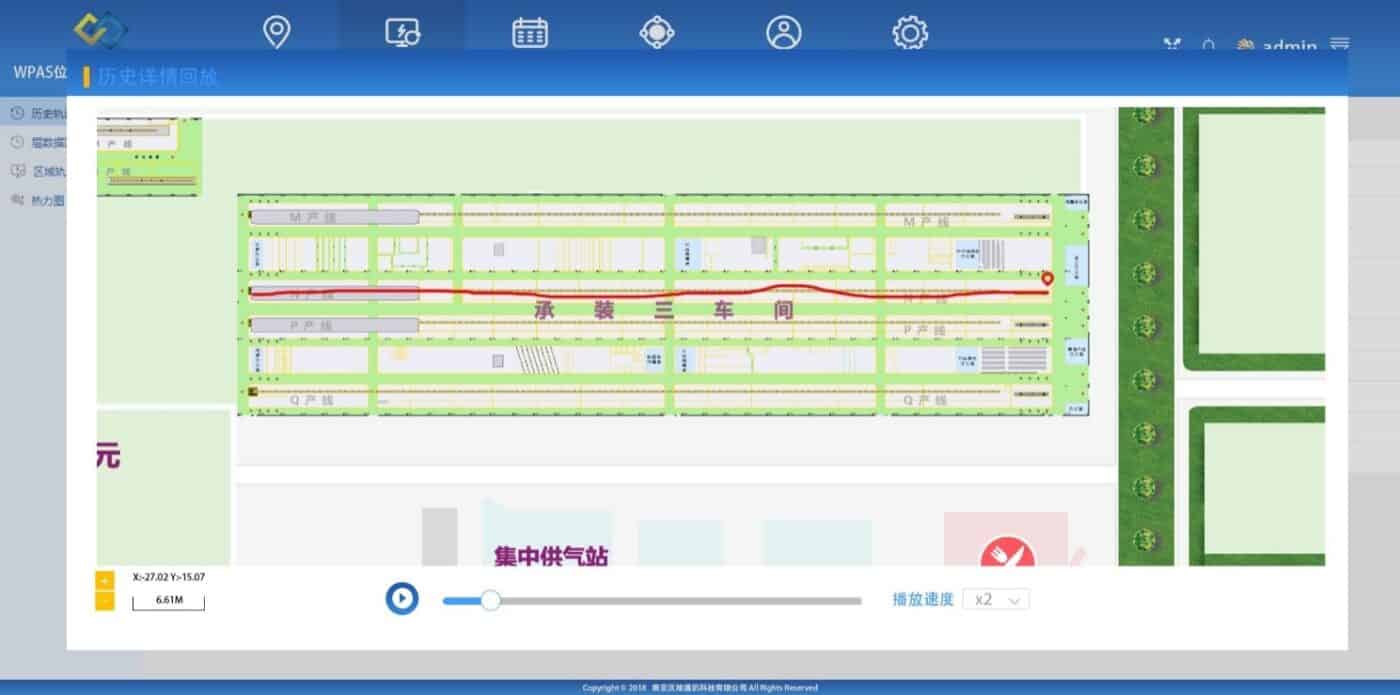
historical trajectory
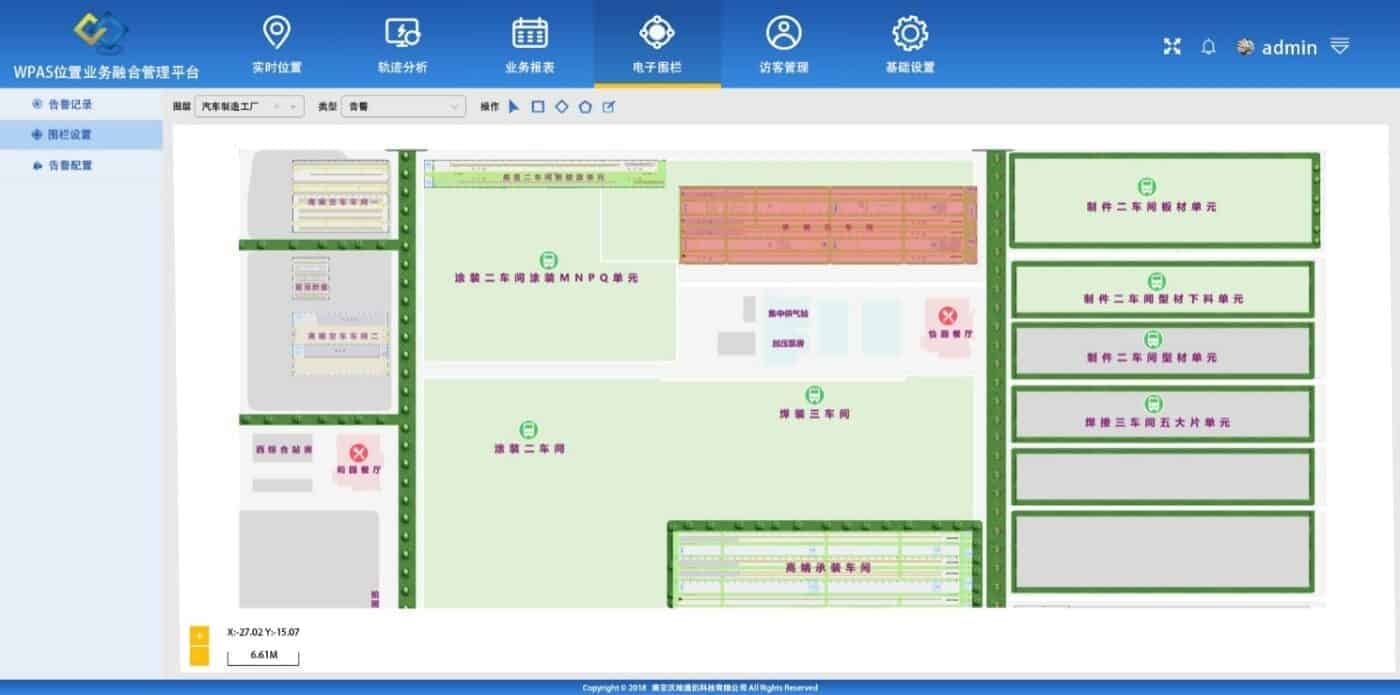
Regional statistics
UWB tags
1. Relevant specification: 802.15.4a
2. Battery type: non-rechargeable lithium manganese batteries
3. Refresh rate: 0.1~20Hz (adjustable)
4. Operating frequency band: 3.24GHz ~ 6.74GHz (Channel 1/2/3/5)
5. Endurance: >1 年@0.5Hz
6. Audible and visual alarms: support
7. Operating temperature: -20 to 60°C
8. Operating humidity: 0% to 90% non-condensing
UWB Outdoor Reader
1. Relevant specification: 802.15.4a
2. Operating frequency band: 3.24GHz ~ 6.74GHz (Channel 1/2/3/5)
3. PoE power: IEEE802.3af/at
4. Networking: wired
5. Protection class: IP67
6. Operating temperature: -40 to 80 degrees Celsius
7. Operating humidity: 0% to 90% non-condensing
Contacts
ContactsContent review.