Application Background
With continued advances in industry and the Internet, fastener distributors and large advanced manufacturing companies are gradually adopting the Vendor Managed Inventory (VMI) model. Fasteners, such as screws and nuts and other non-standard components, are widely used in these businesses. the core of VMI is that based on minimum and maximum levels of inventory and demand forecasts, replenishment is arranged autonomously by the fastener distributor to ensure that the inventory is always maintained within reasonable limits to achieve the desired service level.
Through standardized processes, VMI simplifies the traditional transaction model between fastener distributors and large manufacturing companies, reducing transaction costs and effectively reducing inventory throughout the supply chain. Taking into account the fastener variety, different specifications, and many for non-standard customized parts, the implementation of VMI significantly improves the level of customer service, so that when the demand arises, the customer can quickly obtain the required materials. At the same time, VMI also effectively reduces inventory pressure in the fastener procurement process.
At present, most assembly-oriented enterprises need a large number of fasteners, because of its small size, rich categories and huge consumption, often facing many challenges in management. For example, the workers themselves to receive materials, manual distribution inconvenience, unit price is not high but the consumption of unknown and other issues, making the enterprise in the material management of many pain points. Here are some common problems:
- High purchasing cost: Due to the inability to grasp the purchasing demand, resulting in repeated orders, causing a large number of material stagnation.
- Serious loss due to material breakage: Fastener inventory cannot be grasped in real time, and there is a risk of material breakage, which may lead to production line shutdown.
- High inventory costs: Excessive stocking of inventory takes up space and cash flow, resulting in high inventory costs.
- Untimely data: Long material data inventory cycle, time-consuming and laborious statistics, resulting in increased risk of material shortage.
- Waste of collation: Workshop collation is random and unrecorded, resulting in serious waste and complicated manual application and approval process.
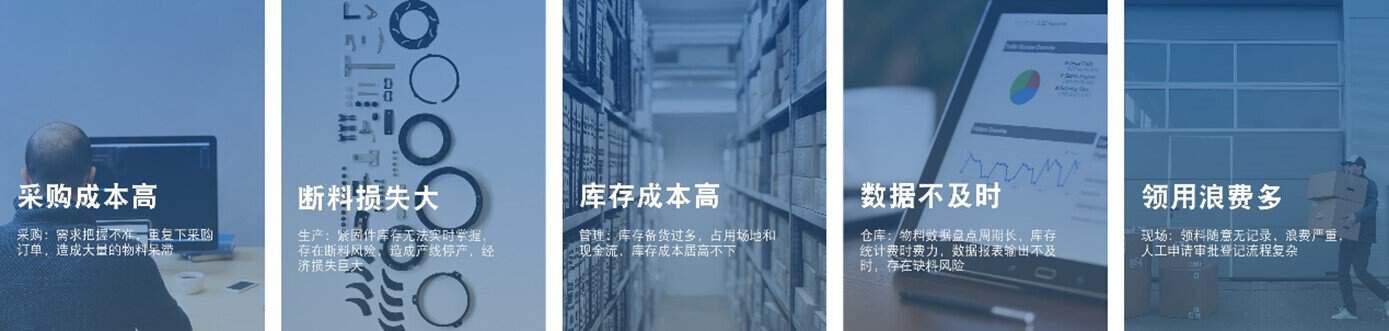
prescription
In order to solve these problems, Seiden Technologies designed a smart racking system for fastener distributors. The system allows distributors to place smart racks on-site at large manufacturing facilities and store a wide range of fasteners and related equipment. The smart shelf is able to count the inventory quantity in real time and upload the data to the software management backend, helping the distributor to arrange replenishment independently according to the inventory level and demand forecast, thus simplifying the purchasing process and enhancing the cooperation stickiness with customers.
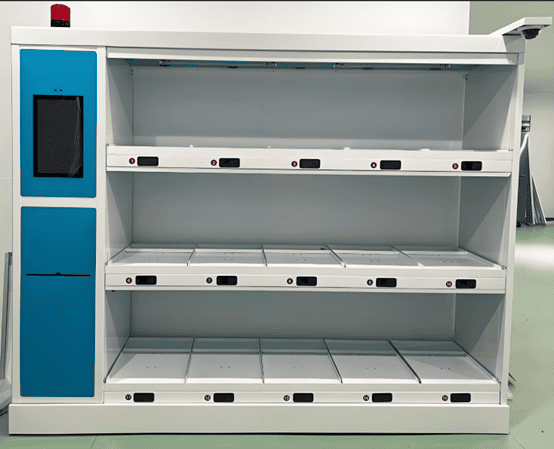
Hardware Products
Intelligent tools inventory shelves give full consideration to the actual needs of equipment management, adhering to the concept of safety, efficiency and convenience, and realizing the perfect integration of perception and identification. The system helps equipment management users to cross into the new era of Internet of Things and digital management through efficient and flexible organization.
Managed materials: screws, nuts, flanges and other fasteners.
Able to solve the problem:
- privilege control
- accurate counting
- automatic settlement
- safe and reliable
- FIFO
- Rapid capacity expansion
- High-frequency use of replenishment alerts
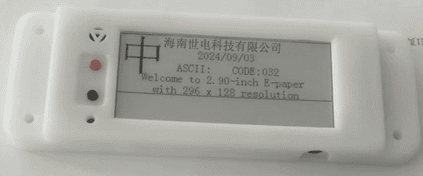
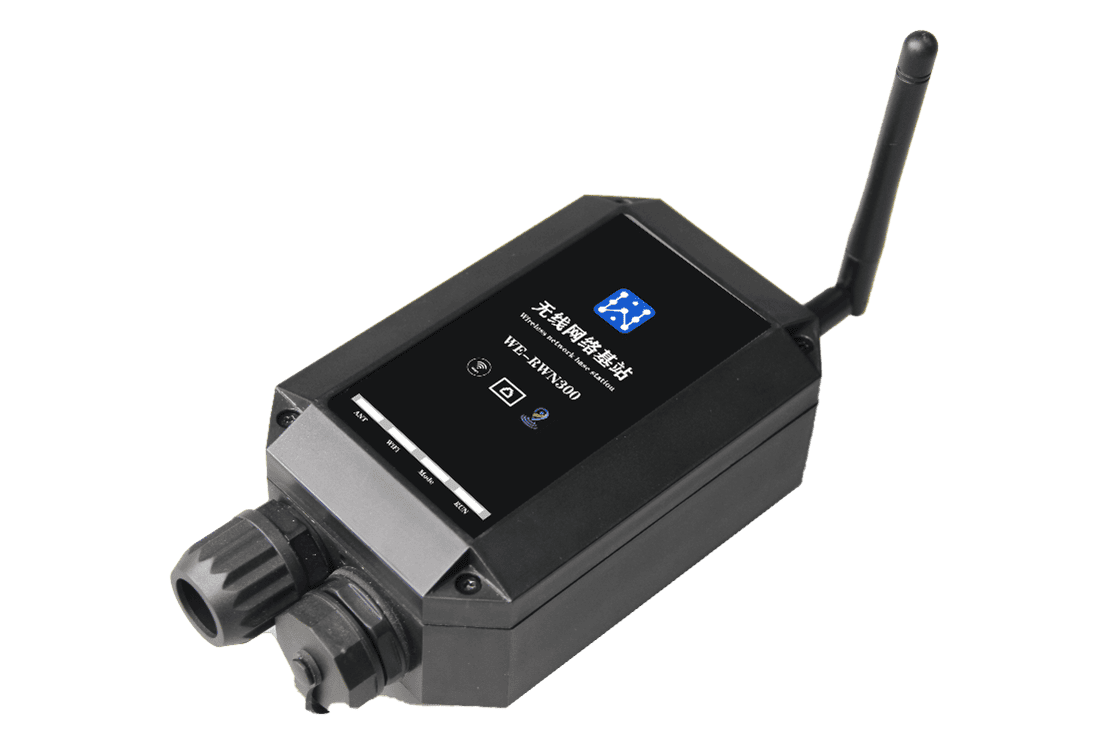
customer value
- Remote monitoring: Realize unattended and rapid remote billing. Accurately monitor the number of pickups and inventory status through gravity detection technology, and the pickup information is automatically uploaded to the software management system after the process is completed.
- Intelligent replenishment management: Upon receipt of a replenishment order, the system can integrate shipping and delivery arrangements to ensure timely distribution of fasteners to the production line's smart shelves.
- Accurate Demand Forecasting: Reduce safety stock levels by analyzing historical data to accurately determine order lots and reduce forecast uncertainty.
- Improved timeliness of delivery: Fastener distributors are able to respond more quickly to the needs of large manufacturing companies, improve service levels and increase customer satisfaction.
Through this smart racking solution, the cooperation between fastener distributors and large manufacturing companies will be closer, achieving continuous optimization and innovation in supply chain management.
Content Reviewer:Jimme Yao