i. program overview
With the intensification of competition in the manufacturing industry and the constant changes in market demand, workshop production progress process monitoring has become an important part of manufacturing enterprises to improve production efficiency, reduce costs and realize timely decision-making. In this context, the workshop production progress and process monitoring module of Manufacturing Execution System (MES) has emerged. By deploying ZigBee dual-frequency tags on materials, equipments and personnel in the workshop, utilizing ZigBee dual-frequency locator and card reader base station to collect data, and integrating with the MES system, it realizes the accurate monitoring of the production progress and process.
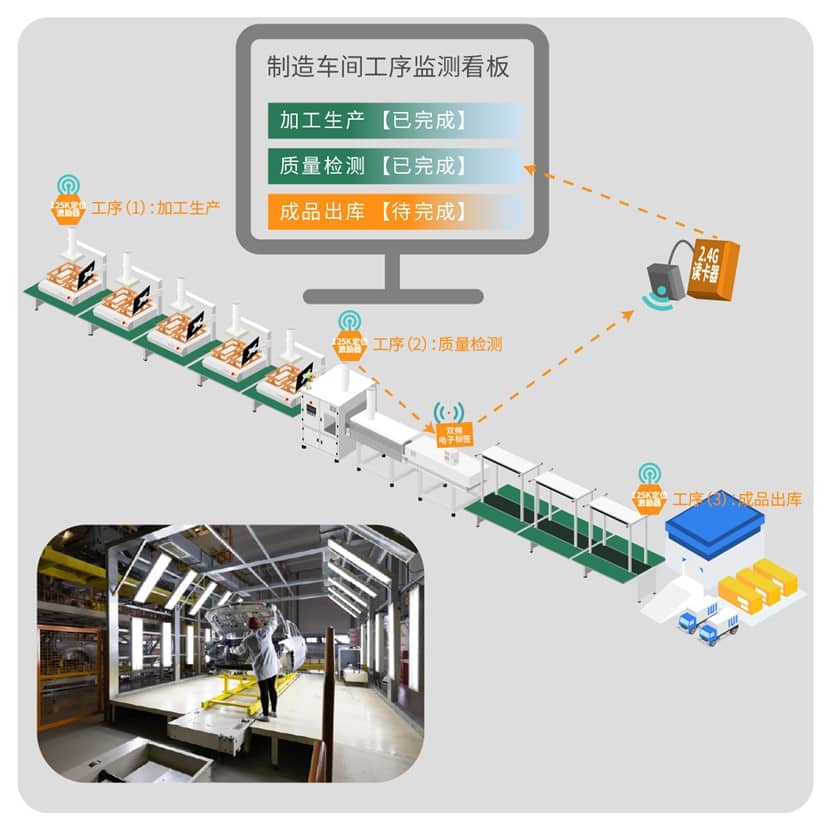
II. Implementation
- label deployment
- Material Labeling: Unique ZigBee dual-frequency tags are affixed to each raw material and semi-finished product, and the tag ID is bound in the software with the stored material number, batch and other information.
- Device Tags: ZigBee dual-frequency tags are installed on production equipment, and the tag ID binds the device number, maintenance information, etc. in the software.
- Personnel tags: Employees wear ZigBee dual-frequency work tags, and the tag ID binds personal identification information in the software.
- dual frequencyCard Reader Installation
- ZigBee dual-frequency locators and card readers are installed at key locations such as workshop entrances, process handover points, warehouse entrances and exits.
- For example, readers at process handover points can automatically recognize the arrival and departure of materials, triggering process changeover records.
- MES System Integration
- Data transmission: Real-time transmission of data collected by ZigBee dual-frequency readers to the MES system.
- Process Monitoring: The MES system determines the start, conduct and end time of a process according to the flow of materials and the use of equipment. For example, when an item with a specific material label arrives at the working area of a process, and the corresponding equipment starts to work, the MES system records the start of the process; when the material leaves the area, the MES system records the end of the process.
- Production Progress Calculation: The MES system calculates the overall production progress based on the completion of the processes. For example, if a product has 10 processes and 6 processes have been completed, the production progress is 60%.
- Exception handling
- The MES system raises an alarm if a material remains in a process for too long.
- In case of equipment failure, through the association of personnel license plate and equipment label, it can quickly locate the employee who was operating at that time, making it easy to trace and solve the problem.
III. Analysis of benefits
- Improve productivity: Accurate process monitoring reduces waiting time between processes and improves overall productivity.
- Quality Traceability: It is convenient to trace the production of products in each process, which is favorable for quality control.
- Real-time monitoring: Management can understand the production progress in real time, and make timely decision-making adjustments.
Workshop production progress monitoring MES system plays a key role in modern manufacturing industry, which improves production efficiency, resource utilization and production quality through real-time monitoring, scheduling and data analysis. By effectively managing and optimizing the production process, companies can achieve higher productivity, faster lead times and higher customer satisfaction. Therefore, workshop production progress monitoring MES system is one of the most important tools for manufacturing enterprises to realize intelligent manufacturing and enhance competitiveness.
Content Reviewer:Jimme Yao