summarize
PROFINET consists ofPROFIBUS International(PROFIBUS International, PI) launched, is a new generation of automation bus standard based on industrial Ethernet technology. It is an automation bus standard based onEthernetIt has the same characteristics as standard Ethernet, such as full-duplex, multiple topologies, etc., and its speed can be up to 100 Gigabit or Gigabit. In addition, it has its own unique features, such as: real-time data exchange, a real-time Ethernet; compatible with the standard Ethernet, can be grouped together; can be seamlessly integrated into the existing fieldbus through the way of proxy.
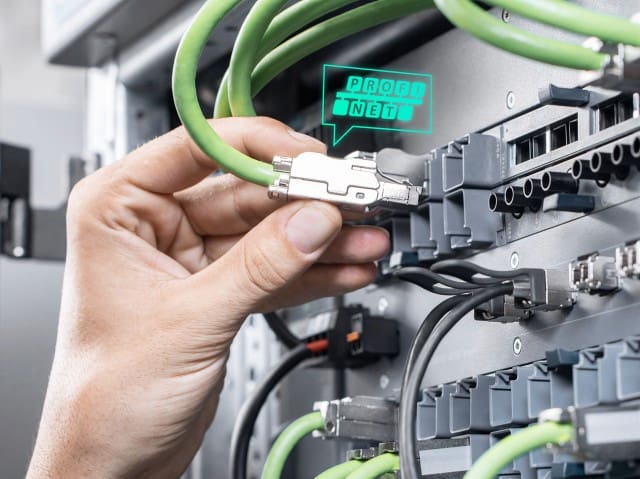
PROFINET offers a complete networking solution for automation communications, encompassing current automation topics such as Real-Time Ethernet, Motion Control, Distributed Automation, Fail-Safe, and Cybersecurity, and, as a cross-vendor technology, is fully compatible with Industrial Ethernet and existing fieldbus (e.g., PROFIBUS) technologies. PROFINET is fully compatible with Office Ethernet and utilizes all the functions of Office Ethernet. However, there are differences, and Office Ethernet cannot provide real-time performance for industrial automation. Office Ethernet is also less able to withstand harsh industrial environments
What is it?PROFIBUS
The benefits of fieldbus include the ability to connect multiple devices via a single cable or "bus". This alone can reduce design, engineering, commissioning and maintenance costs by as much as 40%. The greater accuracy of "digitization" can also mean significant improvements in production speed and quality, while better diagnostics allow fieldbus-connected production lines to benefit from advanced asset management techniques. Fieldbus also provides the real-time performance required in today's automation environments.
PROFIBUS, the world's most widely used fieldbus, was first promoted by the BMBF (German Ministry of Education and Research) in 1989, then used by Siemens and standardized according to IEC 61158. It is supported by more than 1,400 equipment suppliers worldwide. The single standardized approach means that users have a wide choice of suppliers and products, factors that encourage higher performance and lower costs. Fieldbus-enabled plants can also provide more and better data to the monitoring system to support improved management strategies across the enterprise.PROFIBUS is the protocol standard for fieldbus communication in automation technology.
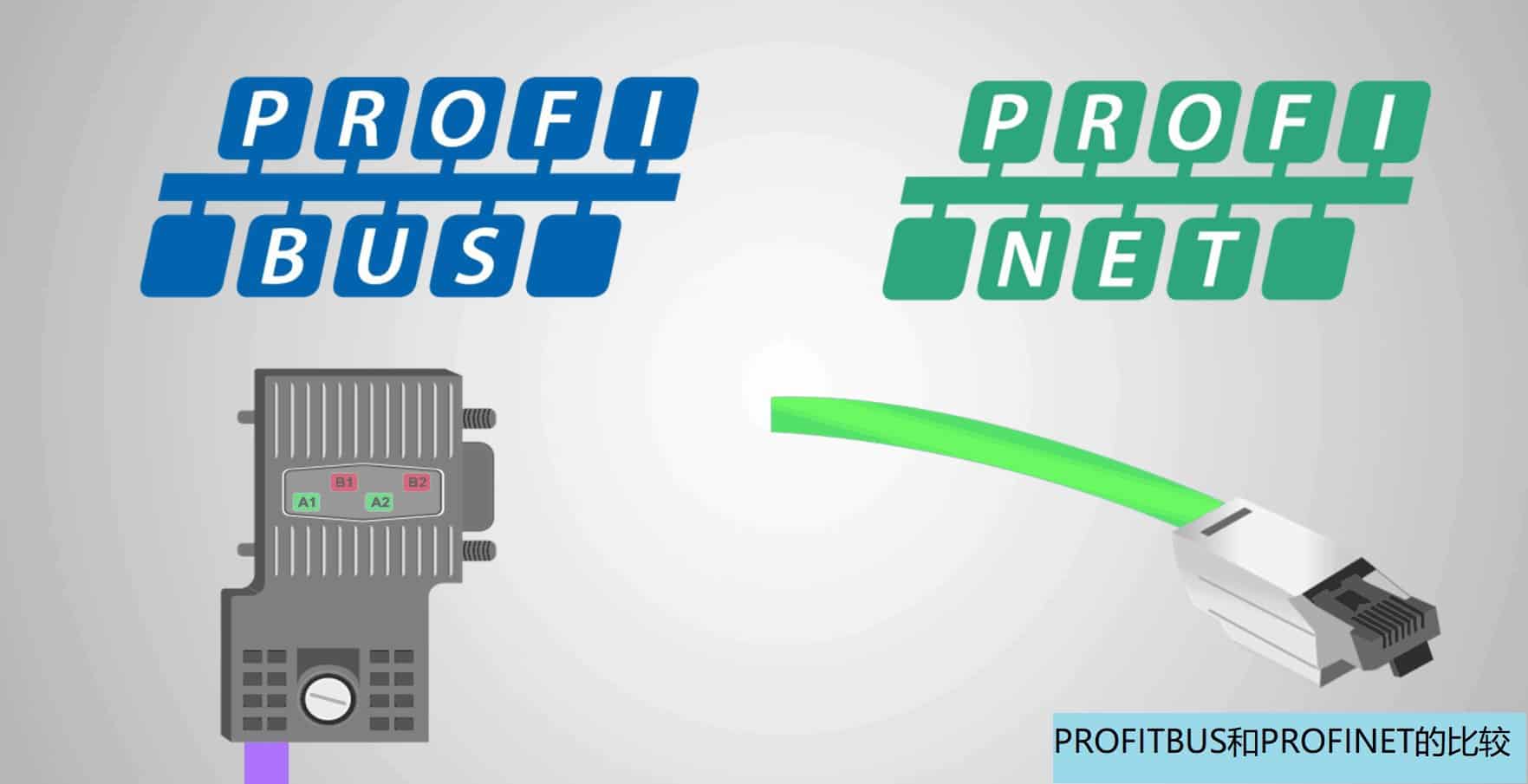
sports event | PROFIBUS | PROFINET |
physical layer | RS-485 | Ethernet |
tempo | 12Mbps | 1Gbps or 100Mbps |
Maximum block size | 244 bytes | 1440 bytes |
Number of equipment | 126 | limitless |
reticulation | master/slave | provider/consumer |
wireless environment | Yes, but the criteria are vendor specific | Wi-Fi, Bluetooth |
PROFINET main features
- With its integrated, Ethernet-based communication, PROFINET fulfills a wide range of requirements, from data-intensive parameter assignment to extremely fast I/O data transfer. PROFINET thus realizes real-time automation and provides a direct interface to the IT level.
- PROFINET is a "switched" network with a transmission rate of 100 Mbps when a full-duplex connection exists. PROFINET is Ethernet-compatible according to the IEEE standard 100% and can be adapted to the existing plant thanks to its flexible wiring, ring and star structure, and copper and fiber optic cable solutions. PROFINET networks can be adapted to the communication needs of the application. PROFINET saves expensive customized solutions and enables wireless communication with WLAN and Bluetooth.
- Communication takes place over the same cable in all applications, from simple control tasks to demanding motion control applications. For high-precision closed-loop control tasks, time-critical process data with a jitter of 1 μs can be transmitted deterministically and synchronously.
- PROFINET integrates automatic response redundancy solutions and intelligent diagnostic concepts. The acyclic diagnostic data transfer provides important information about the status of the network and devices, including a display of the network topology. The defined concept for media and system redundancy significantly increases plant availability.
- The proven PROFIsafe safety technology of PROFIBUS is also available in PROFINET. The ability to use the same cables for standard and safety-related communication saves equipment, engineering and setup.
- Since its introduction in 2004, PROFINET technology has been used by a wide range of companies in all industrial sectors - either in combination with fieldbus systems such as INTERBUS or as a stand-alone solution.
Development History
- PI was founded as PROFIBUS International and its roots go back to the beginning of PROFIBUS in 1987.
- In 2002, PROFINET CBA (Component Based Automation) became part of the international standard IEC 61158 / IEC 61784-1. The basic idea behind Profinet CBA is that, in many cases, it is possible to divide the entire automation system into autonomously operable - and therefore manageable - subsystems. - therefore manageable - subsystems
- In 2003, the first Profinet IO (IO = Input-Output) was released. the Profibus DP (Decentralized Periphery) application interface was successful in the marketplace and was complemented by current protocols for the Internet.
- In 2004, extensions with synchronous transmission followed, which made Profinet IO suitable for motion control applications
- In 2006, Profinet IO became part of the international standard IEC 61158 / IEC 61784-2
- In 2019, Profinet's specifications were finalized along with TSN (Time-Sensitive Networking), standards that define time-sensitive mechanisms for transmitting data over deterministic Ethernet
PROFIBUS International is the oldest and largest fieldbus organization, with 1,400 members, and consists of 25 Regional PI Associations (RPAs) around the world with 32 Competence Centers and 7 certified test labs. In addition to PROFINET, PI supports the largest installed base of fieldbus nodes. PROFIBUS
Protocol Architecture
PROFINET communication channels
We have different ways of communicating in our daily work, one type is with we spend time with our peers in a project, we know each other very well about the scenario that the other person is in now, so in communication we may send text messages or emails in very short language; but if we are dealing with a colleague in the upper two levels or in other departments, we don't actually know what the other person is doing to each other, so we need to have a topic in our communication. There is a theme and our communication must contain a lot of such background information and material.
Like human communication, PROFINET has two different communication channels, one for communicating with peers with whom you share some common "context" (RT), and one for communicating with people with whom you share too much "context" (NRT ).
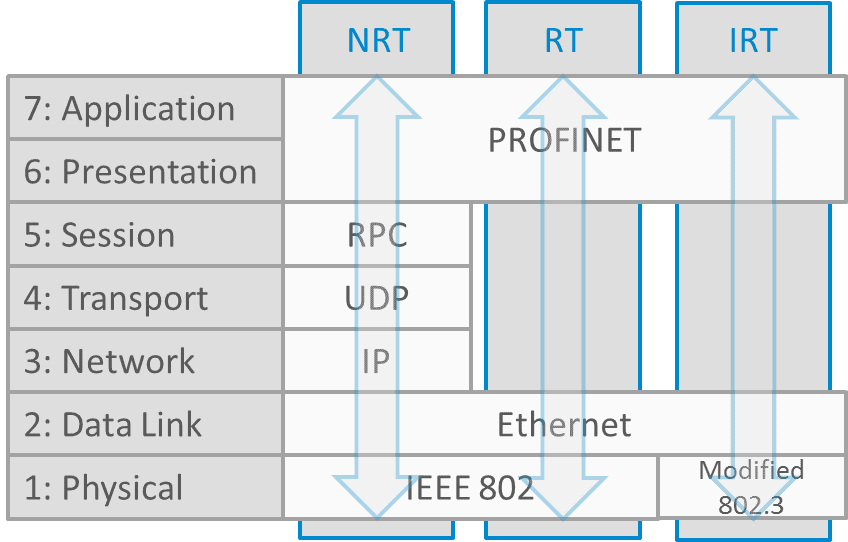
Real-time (RT) channel, which introduces a software-based real-time approach and reduces cycle time to approximately 10ms

Non-real-time (NRT) channels that provide access to specialized access networks through proxies that bridge Ethernet and Bafibus by invoking a TCP/IP remote program. It has a cycle time of about 100 ms and is mainly used for parameter data and cyclic I/O. Typical applications include infrastructure and building automation.

Synchronous Transfer Real-Time (IRT) Channel: is a synchronous real-time technology that requires special hardware to reduce the cycle time to less than 1 millisecond in order to provide sufficient performance for motion control operations over real-time industrial Ethernet
PROFINET Device Type
PROFINET generally consists of the following three types of devices:
- IO Controller (IO-Controller) for controlling automated tasks.
- IO devices (IO-Device) is a field device that is monitored and controlled by an IO controller. an IO device can consist of multiple modules and submodules.
- IO Monitor (IO-Supervisor) is typically PC-based software for setting parameters and diagnosing individual IO devices
Related resources
- PROFIBUS & PROFINET International (PI)
- PROFINET Technology Page
- PROFIBUS International
- PROFINET University
- PROFIsafe web portal
- p-net - an open source PROFINET device stack
- PROFINET System Description and Applications (PDF)
Content review.