I. Industry status and needs
The production line is composed of a series of equipments for producing cement in cement factory: it is mainly composed of crushing and pre-homogenization, homogenization of raw material preparation, preheating and decomposition, sintering of cement clinker, and cement grinding and packaging processes. In the process of cement production line, each production of 1 ton of silicate cement at least 3 tons of grinding materials (including various raw materials, fuels, clinker, mix, gypsum), according to statistics, dry cement production line grinding operations need to consume power accounted for more than 60% of the whole plant power, of which the raw material grinding accounted for more than 30%, the coal mill accounted for about 3%, the cement grinding accounted for about 40%. The cement plant has the following application pain points in the process of production management:
Pain Point 1:Cement production, oil refining and chemical enterprises belong to high temperature, high pressure, flammable, explosive, toxic hazardous industries, coupled with large-scale production equipment, intensive, complex production processes, production processes closely coupled and other characteristics, and discrete manufacturing industry compared with a greater risk. And process-oriented manufacturing production equipment, production workers in large numbers, once the accident, will cause incalculable losses. So how to strengthen control and reduce the probability of dangerous accidents has been the modern process-oriented manufacturing industry facing problems. In the past, the traditional production management personnel safety using the method of access to the camera video surveillance to find the location of personnel to protect the safety of production workers, this technology may be dangerous dead ends, control blind zones, supervisors can not always focus on more than one camera monitoring screen and other issues.
Demand 1:In order to protect the production safety of process-oriented manufacturing workers and improve the management level, the use of advanced positioning technology combined with traditional control methods for operation control, improve control coverage, eliminate blind spots, and multi-departmental managers can remotely access the information and status of field workers.
Pain Point 2:In the case of production operations and poor control of outsiders, due to the complexity of the environment of the production site, which can lead to accidents in the field workers mistakenly enter the danger zone, the monitoring room managers need to always watch the video surveillance of the scene on the big screen, the site operation supervision also need to assign security personnel. When there are simultaneous operations in multiple areas, it will consume more manpower to carry out monitoring, and may lead to accidents due to negligence in supervision.
Demand 2:In order to enhance the efficiency of supervision and control of operations, the use of advanced positioning technology to carry out operational control, the realization of electronic fences and alarm positioning function. Relative to the previous traditional production management personnel safety using dedicated personnel post to view the site of the dangerous areas of video surveillance methods to ensure the safety of production and operation personnel, there may also be carelessness and negligence of management personnel resulting in danger and security accidents, the introduction of advanced positioning technology to solve and optimize the site of the construction personnel in the production of the production period into the prohibited areas of the security of the risk of life, once a non-authority personnel Once a non-authorized person breaks in, an alarm message will be generated on the field personnel management platform, and the management personnel in the monitoring room can immediately know and notify the security personnel on site to check the situation, and the labels worn by the on-site operators and field operators will immediately generate vibration prompts for alarms, which ensures the convenience of management and the safety of the on-site operators.
Pain Point 3:Site inspection personnel to ensure the normal operation of the plant, timely detection of equipment and the site of hidden dangers and dangerous situations, so as to solve and eliminate the situation so that the plant works in a normal and orderly manner. Inspection staff should be on time according to the requirements of the whole plant section of each location for inspection run check. At present, the traditional on-site inspections, most of the on-site inspections for the operators to sign their own registration inspection time and records, there is a timeliness of not timely and personnel instead of each other inspection problems.
Demand 3:By joining the positioning technology to realize the inspection management function, combining the traditional inspection method and personnel positioning with each other, the on-site inspection management personnel can set up each inspection point in the factory in advance, and also can set up the order of different inspection points, so that the on-site operation personnel inspection is more intelligent and more convenient, and whether the inspection personnel complete the inspection work on time or not, solving and optimizing the timeliness of the inspection management and ensuring the accuracy of the inspection personnel. The accuracy of the inspection personnel.
II. Overall programmatic structure
The system includes UWB tags, UWB outdoor wired base station, positioning engine software (C/S architecture) and positioning application system. Positioning tags and positioning base station communicate through UWB pulse signals. The positioning base station transmits the received data from positioning tags to LS1000 positioning engine through 5G network and wired Ethernet for data analysis and processing, and transmits the processed accurate position to the upper layer application through an open API interface.
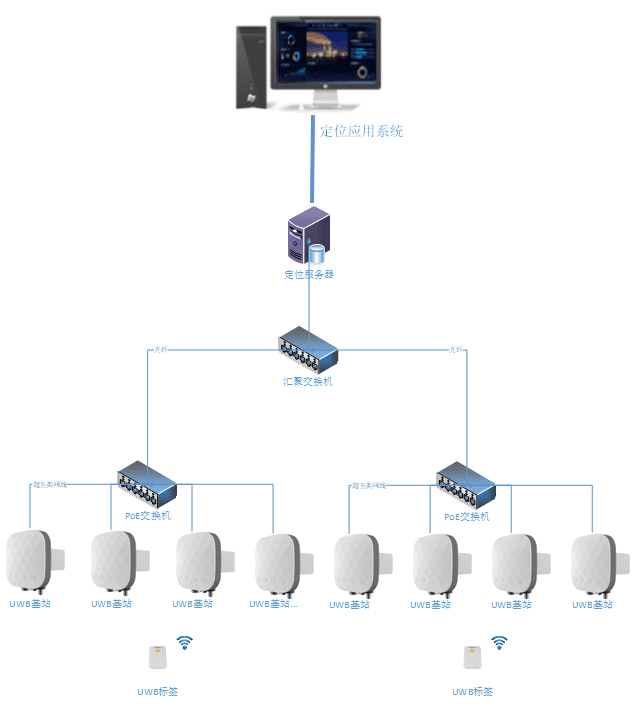
The system components are as follows:
- UWB tags: card-type and wristband-type, fixed on top of the person or object to be located, can periodically transmit UWB signals with tag ID information.
- UWB outdoor wired base station: communicates with the positioning tags and transmits information back to the positioning engine algorithm software;
- Positioning engine algorithm software: locally deployed, the underlying information data is collected and processed through the algorithm of the positioning engine to get the accurate coordinates of the positioning tag.
- Positioning application software: locally deployed or cloud deployed, the application layer software realizes the basic functions such as positioning display, track playback and other functions, as well as the business functions such as electronic fence, intelligent inspection, attendance statistics and video linkage based on the expansion of location data.
III. On-site deployment
Based on the plant area to be covered by this cement plant, the feasible BTS deployment plan is evaluated in conjunction with the drawings and site survey, as shown in the following figure:
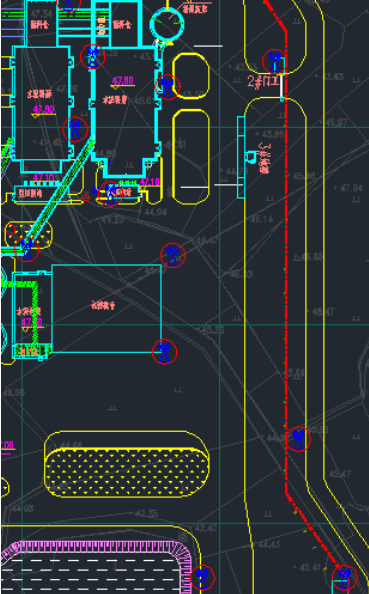
After the program has been reviewed and approved by many parties, it enters the construction stage (the integrator is responsible for construction and installation, and Hainan Shidian guides the installation and debugging), and the base station is installed to the designated location in accordance with the design program, and the installation of the physical picture is as follows:
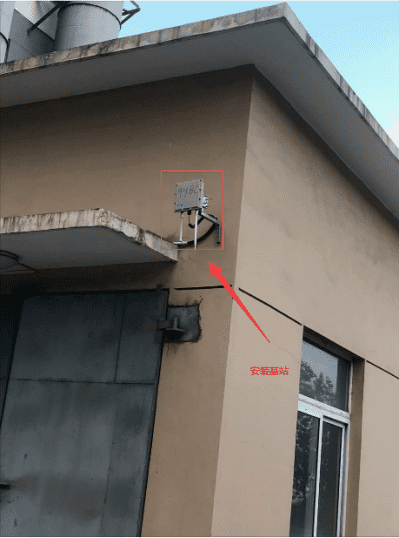
Positioning Application Platform Software Demonstration
The platform software can count the number of people in each area in real time, such as limestone crushing workshop, cement powder workshop, waste heat power plant room, general control room, outdoor cement emanation plaza and so on. It builds a visualization, integration, intelligent three-dimensional digital intelligent control platform, which improves the comprehensive management efficiency of safety production in the plant, and the personnel safety management efficiency is improved by more than 20%.
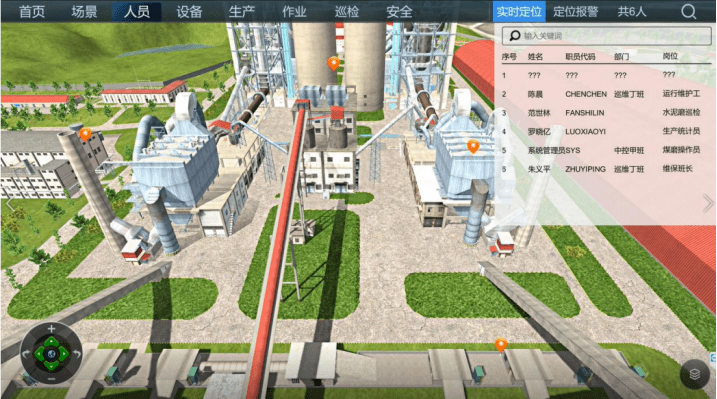
Content review.