I. Programmatic background
In today's competitive manufacturing environment, efficient and accurate factory management is critical to the survival and development of an organization. Tooling management is in turn one of the key aspects of manufacturing plant operations, however, traditional management methods often suffer from a number of problems that lead to inefficiencies, increased costs and inconsistent quality.
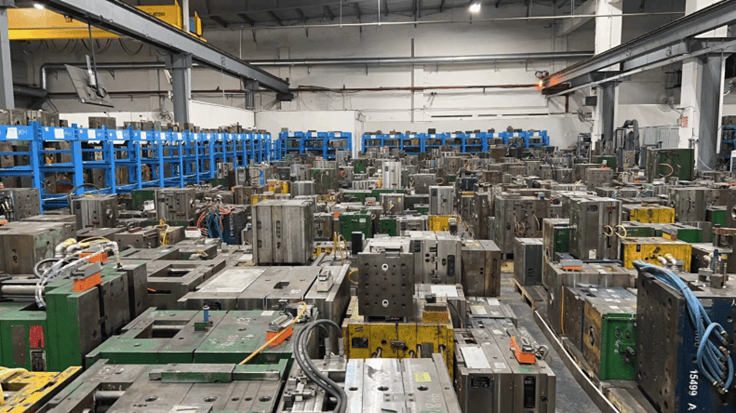
☛ Mold management pain points
- Molds are numerous and valuable:
A medium-sized factory may have thousands of sets of molds, each costing from a few thousand dollars to hundreds of thousands of dollars. According to statistics, one factory has 5,000 sets of molds with a total value of more than 50 million dollars.
- Molds are used frequently and are difficult to maintain:
The average number of times a mold is used per week can be more than 20 times, frequent use of the mold leads to easy wear and damage. Take an injection mold as an example, after 5000 times of injection, it needs to be overhauled, and the maintenance cost is as high as 5000 yuan.
- Molds are disorganized and difficult to locate:
The traditional manual recording and management method makes the search and deployment of molds take a long time, and it takes more than 30 minutes on average to search for molds each time, which seriously affects the production efficiency.
- The mold history is not clear and the service life cannot be accurately assessed:
Due to the lack of effective tracking means, it is impossible to accurately grasp the number of times the mold is used, the number of repairs and other key information, resulting in the inability to timely replace the aging mold, affecting product quality.
Second, ZigBee technology solutions
- Mold Identification and Traceability
ZigBee tags are installed for each set of molds, and the tags are bound to the mold's number, name, specifications, production date, number of times used, number of times repaired, and other information. Install read-write in the storage area of the mold and the use of equipment to read the location and status information of the mold in real time. Through the system software to find the required mold model, view the location of the mold in the software map, and then call the tag near the map location, according to the tag sound and light prompts to quickly find the required mold, improve work efficiency.
Actual data: After the implementation of ZigBee mold management system in a factory, the search time for molds was shortened from an average of 30 minutes to less than 5 minutes, and the production efficiency was increased by 80%.
- Mold Maintenance and Repair
According to the number of times the mold is used and the number of times it is repaired and other information, the system automatically generates a maintenance plan and reminds the relevant personnel to carry out maintenance work. At the same time, the content and results of maintenance are recorded to provide data support for the full life cycle management of the mold.
Actual data: After the implementation of ZigBee Mold Maintenance Management System in a factory, the average service life of the molds has been extended by 30% and the maintenance cost has been reduced by 20%.
- Mold Life Evaluation and Early Warning
By analyzing the usage data of the molds, the remaining life of the molds is evaluated and an early warning is issued when the molds are close to their life expectancy, reminding the management to replace the molds in time to ensure the quality of the products.
Actual data: After the implementation of ZigBee mold life assessment system in a factory, product quality problems due to mold aging were reduced by 70%, and the customer complaint rate was reduced by 50%.
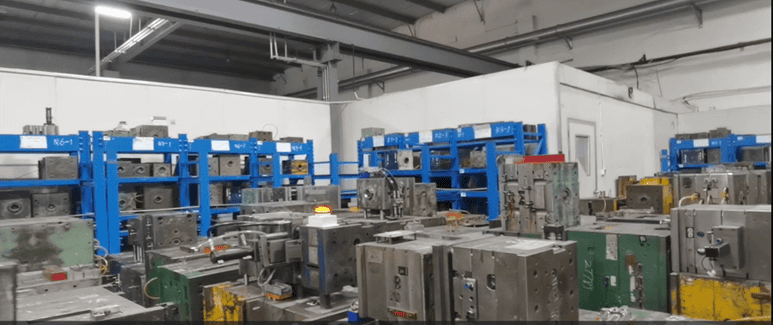
III. Programmatic structure
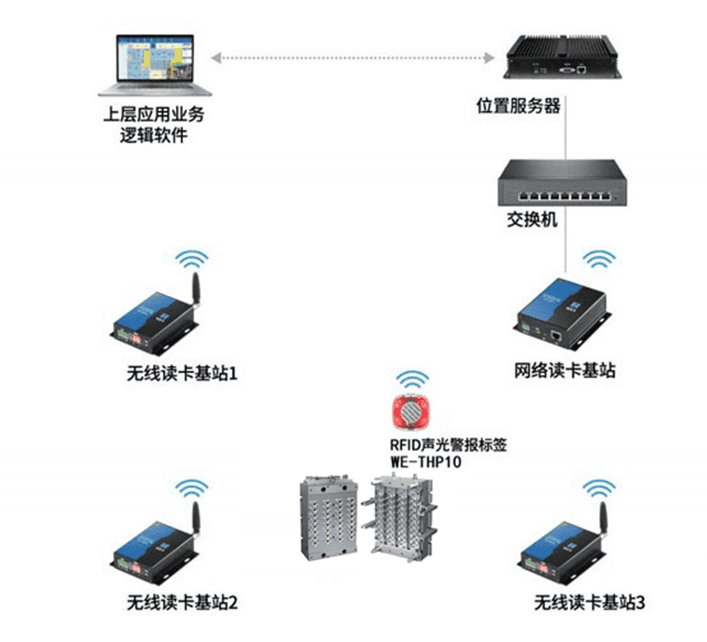
IV. ZigBee System Implementation Steps
(i) Needs analysis
Gain an in-depth understanding of the factory's production process, management model and business requirements, and identify the problems to be solved and the desired goals. Communicate and research with related departments and personnel to collect data and information to provide basis for system design.
(ii) System design
Based on the results of the requirement analysis, design the overall architecture, hardware device layout, software function module and data flow of the ZigBee system. Select appropriate hardware devices such as ZigBee tags, readers, antennas, etc., and determine their installation locations and methods. Develop the corresponding software system, including database management, data acquisition and processing, business logic control and other functional modules.
(iii) Equipment installation and commissioning
According to the system design scheme, install the ZigBee hardware devices and carry out debugging and testing. Ensure that the equipment can work normally, and the label and item binding information is accurate. At the same time, install and configure the software system, and co-communicate with the hardware devices to ensure the stability and reliability of the system.
(iv) Data collection and integration
Collect relevant data through ZigBee readers and integrate them into the enterprise's information system. The collected data are cleaned, converted and analyzed to extract valuable information to support management decisions.
V. Analysis of costs and benefits of implementation
(i) Implementation costs
1, ZigBee hardware equipment costs: including tags, readers, antennas, location servers, etc., depending on the size of the factory and application scenarios.
2, software system development costs: customized development of ZigBee management software to suit the needs of the factory.
3, the cost of system integration: the ZigBee system and the enterprise's existing information systems for integration.
4. Operation and maintenance costs: including equipment maintenance, data management, system upgrades, etc.
(ii) Benefits analysis
1, improve production efficiency: through the rapid search for molds, reduce inventory shortages, etc., is expected to improve production efficiency 30% or more.
2, reduce costs: reduce mold maintenance costs, inventory backlog costs, product recall costs, etc., is expected to reduce 10% per year.
3, improve product quality: through the mold life assessment, product quality traceability, etc., it is expected that the product qualification rate can be increased by more than 5%.
4, enhance customer satisfaction: timely delivery of products, ensure product quality, customer satisfaction is expected to increase 20% or more.
(iii) Payback period
By implementing the ZigBee technology solution, it is expected that the investment cost will be recovered within 1 year and long-term economic and management benefits will be realized.
Content Reviewer:Jimme Yao